Boston Atomics' Substack
Writing about all things advanced nuclear
Convening authors from all around the industry
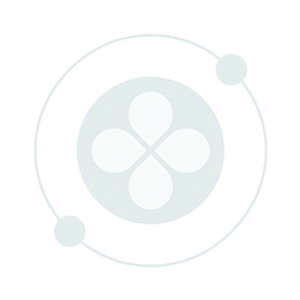
Why the future CANDU Reactor Will Probably Be a Superior Choice Over LWRs for Modern Energy Needs (in most countries)
In the quest for sustainable and efficient nuclear energy solutions, the choice of reactor technology plays a pivotal role.
In the quest for sustainable and efficient nuclear energy solutions, the choice of reactor technology plays a pivotal role. While Light Water Reactors (LWRs) have been the predominant choice for many years, CANDU (CANada Deuterium Uranium) reactors, or more broadly, Heavy Water Reactors (HWRs) present compelling advantages that could make them a superior option for most countries in the coming years. Let's explore why CANDU reactors stand out in the nuclear energy landscape.
1. Fuel Efficiency and Flexibility
One of the most significant advantages of CANDU reactors is their ability to use natural uranium as fuel. Unlike LWRs, which require enriched uranium, CANDU reactors can operate with natural uranium, reducing the need for complex and costly enrichment processes. This not only lowers fuel costs but also makes CANDU reactors accessible to countries without enrichment capabilities. Moreover, CANDU reactors are highly efficient in utilizing fuel. They extract more energy from the same amount of natural uranium compared to LWRs. This efficiency translates to better resource utilization, addressing one of the critical challenges in nuclear energy management.
2. Online Refueling
CANDU reactors offer the unique capability of online refueling. This means that the reactor can be refueled while it is still operating, without the need for shutdown. Minimizing and simplifying the activities that happen during outages, the Availability Factors of a NPP could be increased beyond the about 95% long term ceiling that the industry is used to. However, removing the need to shut down for refueling is not enough, since there are other activities such as inspections that may require the shutdown for maintenance to happen anyway. Nevertheless, online refueling gives the chance of optimizing operations to minimize or remove the other causes of outages. Through this process, online refueling offers an opportunity to improve Capacity Factors.
On the other hand, we should also mention that CANDUs have the outages due to refurbishments, that would reduce effective Availability Factors from their startup date to decommission. Refurbishment times can also be optimized, but in all fairness to LWRs we should mention that they don’t need to deal with as complex refurbishments as CANDUs (although when life extensions happen in LWRs, some components and parts are typically replaced, leading to some outages as well).
AP1000s (LWRs) are gen 3+ reactors very well-optimized for smooth operation and high Availability Factors. Since they have started operating worldwide, they have delivered better Availability Factors in general than the HWRs we have today. However, the CANDU fleet that we have today in the world is all gen3 or lower. I am optimistic that the next CANDU design iterations will be able to improve Availability Factors with respect to the CANDU reactors in operation today.
3. Energy Independence
In today's world, where relationships between companies, governments, stakeholders, and customers can be strained and competitive, achieving energy independence is crucial. Many countries do not have the capability to enrich uranium, making them reliant on external suppliers. This dependency can be risky, especially if the supplier has significant leverage or influence, which is often the case in geopolitical contexts.
Heavy Water Reactors (HWRs), such as CANDU reactors, offer a valuable solution. These reactors can use natural uranium, eliminating the need for enrichment. This independence from uranium enrichment not only reduces costs but also minimizes the risk of being pressured or bullied by suppliers.
For countries that cannot enrich themselves and already have an operating nuclear fleet with enriched uranium, factors such as economies of scale, workforce preparedness, and established supply chains may outweigh the energy independence argument. These countries might find it more practical to continue with their existing Light Water Reactor (LWR) technology due to the established infrastructure and trained workforce.
However, for countries that are yet to embrace nuclear power technology for the first time and would benefit from nuclear energy independence, Heavy Water Reactors (HWRs), such as CANDUs, would be preferable, CAPEX aside. For these nations, this plus the added benefits of HWRs in terms of fuel flexibility and safety make HWRs an attractive option.
4. Capital Expenditure (CAPEX) Considerations
While the initial capital expenditure for CANDU reactors has been a point of contention, recent cost trends suggest that the cost difference between CANDU and Light Water Reactors (LWRs) may not be as significant as previously thought. The horizontal orientation of the calandria in CANDU reactors allows for more efficient space utilization and potential reduction in reactor building volume in future design iterations such as MONARK. Additionally, the cost of heavy water, once a major economic disadvantage, is now a smaller fraction of the overall cost due to the high costs of Nuclear Power Plants construction in the West.
i. Efficient Space Utilization
Due to the horizontal orientation of the calandria and associated operations such as refueling, it may make more sense than in an LWR to also orient steam generators (SGs) horizontally or have compact SGs. This results in potential for reactor building (RB) volume reduction leading to a modest reduction in capital cost.
ii. Heavy Water Cost
The cost for "enriching heavy water" used to be a large slice in the CAPEX estimates for CANDUs and also in terms of $/kW, in the case of LWRs. This was pointed out as the main economic disadvantage from CANDUs. This was in a world where large LWRs were projected at $3,000/kW. Then an extra $1,000/kW only for the heavy water seemed like a lot (+33%). However, the West has not proven capable of completing an LWR in this century below $10,000/kW. Assuming the cost of enriching heavy water remains (which is a valid assumption given that the facilities exist, and it is mostly about using energy in the separation process), then the difference comes down to 10%, namely, engineering error. Now the capital cost estimate starts looking much more similar.
iii. Financial Cost
Financial costs (at equal construction duration) should be lower for a Heavy Water Reactor (HWR) than for an LWR given the risk of relying on an external Low Enriched Uranium (LEU) supplier is gone. This independence from external suppliers reduces financial risk and should lead to more stable and predictable capital costs.
Conclusion
While LWRs have served the nuclear energy sector well, the advantages of CANDU reactors make them a superior future technology of choice in many places. Their fuel efficiency, online refueling capability and potential for greater energy independence position CANDU reactors as a forward-thinking solution for countries aiming to achieve sustainable and efficient nuclear energy.
As the world continues to seek cleaner and more reliable energy sources, embracing CANDU technology could be a pivotal step towards a brighter and more sustainable future.
Call to Action
AtkinsRealis: Please deliver and promote your technology. Consider innovative designs and arrangements to enhance the efficiency and appeal of CANDU reactors.
Countries: Open your eyes to the benefits of Heavy Water Reactors (HWRs). Each nation has unique conditions, but the pursuit of energy independence (alongside energy security) should be a priority unless there are no viable options.
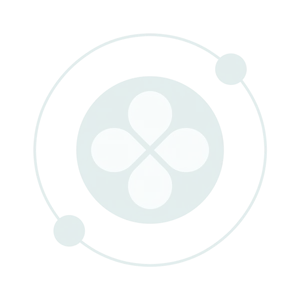
The MIGHTR project
a tale of cycles
Inception and general aspects
The MIGHTR, Modular Integrated Gas High Temperature Rector, is a High Temperature Gas Reactor (HTGR) created to be the natural technical continuation from the Next Generation Nuclear Plant (NGNP) program. While some countries have advanced further in HTGR development in the last decades, those lagging behind could adopt a smarter design strategy rather than replicating or slightly modifying existing models with more resources.
I believed MIGHTR had strong potential because, thanks to the focus on constructability, it represented a logical continuation from the NGNP and MHTGR projects, as well as other HTGR initiatives worldwide. This approach allowed us to build on the extensive work already done in these multi-decade projects, rather than starting from scratch, while modifying some aspects of the design to improve constructability dramatically.
The term HC-HTGR is a general label for the concept, similar to how LPSR refers to the AP1000 or LASR the APR-1400 and similar. MIGHTR was the name we chose for the potential product at the project’s inception.
The inception of MIGHTR began with a heated debate between Robbie and me in the spring of 2019. Our research group at MIT had selected the NGNP design (SC-HTGR) for a technology scoping project aimed at supplying process heat in Japan. While the group was generally enthusiastic about this technology, there was no consensus on its feasibility as a deliverable project. Robbie was initially frustrated with my criticisms of the NGNP design, but eventually, he listened to my arguments and asked, “Alright, help me make this design better. What would you change to address the issues you’re pointing out?”
From that moment, we dedicated hours outside of our responsibilities within the Japan Next Project and any MIT-related activities to sketch a reactor design that could overcome the challenges faced by the NGNP project. When we informed our professors about our extracurricular efforts, they not only encouraged us to continue but also offered enthusiastic support.
A few weeks later, our professors encouraged us to present our idea at a student competition at ICAPP Abu Dhabi in Spring 2020 and at the MIT Energy Night in October 2019. Then we decided to file a provisional for protection in 2019 and the patent application in 2020. We presented the concept at many stages between 2019 and 2021. The culmination was a publication on the Applied Energy journal.
At the start of 2020, we began to develop the MIGHTR concept more seriously. By summer, we had convinced Professor Koroush Shirvan to submit a proposal for a three-year conceptualization project to the US Department of Energy (DOE) under the Advanced Reactor Demonstration Program (ARDP). In December 2020, the DOE announced a $4.9 million funding ward for the development of the MIGHTR/HC-HTGR concept under the ARDP program, ARC-20 track.
We worked independently from the DOE-funded project members until August 2021. From September 2021 onwards, the DOE-funded team joined the project, each member advancing a specific aspect of the design. Over these three years, the development progressed much faster than before.
We are immensely grateful to the DOE for funding this project and to all the participating institutions for their contributions. Special recognition goes to MIT’s leadership. We have summarized all the major aspects of MIGHTR in ANS publications.
ARC-20 overview
The ARC-20 team comprised MIT, UB, UM, MPR Associates, and ANL, with MIT leading the project under the guidance of Professor Koroush Shirvan. Within the consortium, BA subcontracted to MIT, and SGH subcontracted to UB. The consortium began its work in September 2021.
This project encompassed various aspects, including cost modeling, printed circuit heat exchanger development and testing, neutronic design and modeling, shielding and activation analysis, mechanical structural analysis, fabricability, licensability, reactor cavity cooling system thermal hydraulics, core thermal hydraulics, primary system thermal hydraulics, seismic analysis, civil design, and construction assessment.
Tasks outside the ARC-20 project
The work undertaken by BA outside of the ARC-20 project includes:
Refueling and Tooling: We subcontracted Sam Quemby, an engineer with over five years of experience in nuclear robotics. Deft Dynamics and Southern Research (now Kratos SRE) collaborated on projects related to MIGHTR robotics under ARPA-E contract DE-AR0001157.
Integration of Disciplines: We integrated the work of various systems, structures, and components to create a consistent Nuclear Power Plant. Our unique strategy for this integration was published in ANS.
Safety and Licensing: We prepared for NRC engagement to ensure safety and compliance.
Where the MIGHTR is now
Over the past four years, we’ve made significant strides in addressing the major feasibility questions we initially faced. At an early stage of this type of project, it is important to focus on evaluating the feasibility of the different changes proposed with respect to the reference design from where the project starts. This is particularly challenging, for obvious reasons, if it is a white paper project, i.e., there is no reference technology to compare to. In our case, we have the MHTGR design as a reference. Every task faced an array of constraints and objectives, but here is a simplified version of them:
Key Achievements:
Reflector structural mechanics: Objective: show the graphite reflector blocks could last 10+ years to avoid replacement while meeting their dose limits, fabrication tolerances, shielding constraints, structural requirements, interfacing requirements and layout limitations. Avoiding replacement greatly simplifies the operations and design for operations. After three years of iterations, the structural mechanics of the reflector look feasible. While some redesign or block splitting may be needed, our conservative stress assumptions suggest we’re close to our limits.
Core control: Objective: control the core reactivity using only the outer reflector to limit the temperature exposure during design basis events and maintain access for the refueling equipment. Thanks to the work from UM and MIT, we are quite sure we can control the core from the outer reflector, showcasing their exceptional neutronic analysis capabilities.
Seismic advantage: The seismic robustness of the low-rise MIGHTR building, and its reactor primary system and internals, was evaluated using numerical analysis by the team at UB. Two-dimensional and three-dimensional seismic isolation solutions were explored to mitigate the impact of the seismic load case.
Seismic resilience of graphite core: The objective is to deploy a shear-key based design for the graphite assemblies that eliminate the need for dowel pins common to other HTGRs. UB’s seismic testing of the model assemblies demonstrated that the proposed design resists seismic forces through the controlled rotation of the blocks, thus minimizing the bearing stresses on the shear keys. No chipping/damage of shear keys was observed even after many cycles of repeated and rigorous testing with peak base accelerations exceeding as high as 0.8 g. Test videos can be accessed at this link.
Helium leak management: The integrated design of MIGHTR introduces a mid-vessel flange that poses different design loads than the flanges in NGNP. Objective: ensure that this flange can meet helium leakage limits, fabrication requirements, and design loads. Our mid-vessel flange can likely be fabricated to maintain helium leak rates to a limit that does not invalidate the concept, ensuring the design remains practical. If it lost too much helium, the design would be impracticable. We defined feasibility to mean <10X the leakage rate of the Fort St. Vrain HTGR, and we found that a much lower rate is possible. In the future, this aspect should be included in the technoeconomic analysis to identify the exact helium leak rate and where the threshold for acceptable cost is.
Efficiency hit due to by-pass flow: The novel fuel block design and control drums created new bypass flow paths through the core that is not directly or efficiently heated by the fuel. Objective: limit the flow lost through by-pass to minimize wasted helium pumping energy. By-pass flow appears to not result in a show-stopping efficiency drop.
Accident thermal management: Objective: show that temperatures variations during major design accidental conditions are manageable. The back of the envelope analyses we have done show that in a horizontal SMR HTGR, Pressurized Conduction Cooldown (PCC) and Depressurized Conduction Cooldown (DCC) yield much lower temperature differences along internal components (10s of °C) compared to vertical designs (100s of °C), making them easier to manage. In vertical HTGRs, during PCC accidents, the top gets hot because of hot gas accumulation. This poses challenges and requires engineering solutions.
Fabrication and installation: We can likely fabricate, transport, and install all core and primary system components without major issues. Thank you MPR Associates for your assistance at figuring this out.
RCCS performance: The Reactor Cavity Cooling System (RCCS) comprises a set of ducts, panels and tanks that can remove decay heat and protect RPV, internals and civil works around from excessively high temperatures in different accidental conditions. Vertical HTGRs have the benefit of long heating distances to generate enough driving force for natural circulation. The reduced heating height from a horizontal HTGR brought the question at the beginning of the project on whether this would be problematic to guarantee RCCS performance. The work conducted by ANL in the project suggest that the RCCS works well with our reduced height constraint, potentially outperforming vertical HTGRs in some aspects, like dynamic behavior of raiser tubes and panels.
Power output: Our core operates at 150 MWth, with potential to uprate to 200 MWth+ through value engineering and design optimization, enhancing economic viability. This uprate would potentially make MIGHTR the most economical HTGR on the planet, capable of supplying process heat for ammonia, cement, chemicals and many other products. The objective from the project was hitting the 150 MWth, so we were on target.
Refueling machine: Objective: design a machine capable of placing and removing every fuel and inner reflector block every 18-24 months. The refueling machine at this stage is a multi-degree of freedom robotic arm railed to a cantilever beam that retrieves and replaces fuel blocks during refueling. A machine vision scheme shows promise for the refueling machine.
Major Perceived single Remaining Challenges:
Mid-Vessel Flange: Assessing its impact on the economic potential for a MIGHTR in the 150-200 MWth range.
PCHE/HX/Secondary system: Deciding whether to use a Printed Circuit Heat Exchanger (PCHE) or simply a Heat Exchanger (HX) and with what scope plus the integration of this with the rest of the secondary system, as well as planning operation and maintenance of the different valves in the primary system and integration with the circulators. There is a lot of decisions still to be made in ducting, valves, penetrations, thermal expansions management, maintenance, fabrication limitations management, etc.
Refueling/Tooling: Developing specific operation, maintenance, assembly and decommissioning tools for the MIGHTR architecture, which may necessitate redesigning some reactor parts.
Integration:
The most challenging aspect is integrating all these elements into an operable, constructible, licensable, and cost-competitive design.
Where the MIGHTR is going
What would be best for the project now?
1. Specify every system based on the work done
2. Engage with the regulator
3. Start building prototypes
Development is expected to progress slowly. There’s a possibility that MIGHTR may continue its development in Europe. Robbie will be dedicating most of his time to a separate entity focused on LWRs, reducing his involvement in MIGHTR to minimal management duties at Boston Atomics (expect a future post on this).
I will maintain my role at MIGHTR but with a new approach. I will now sign consulting and R&D contracts with companies and institutions, working on projects that benefit both the institution and MIGHTR. This could involve developing micro-reactor HTGRs or assisting with HTGR cost-modeling, all of which will advance MIGHTR and HTGR technology.
For instance, the MIGHTR patent remains open up to 20 MWth, allowing for the possibility of a lower power demo as part of the concept development conducted by an external entity for its own benefit. Any external work on this low-power version would be welcomed and beneficial to the project.
Additionally, I will continue to push the ongoing technical work for MIGHTR, dedicating a fraction of my time to ensure its progress.
Final notes
The MIGHTR project has had ups and downs. In 2019 and 2020 the MIGHTR team was tiny. For 3 years, the project has been relatively big and advanced steadily. Now it looks like the resources into the MIGHTR project are going to be small again. As stated before, I don’t expect to be able to demonstrate MIGHTR at full scale before the late 2030s. However…I am waiting for our opportunity. When the right people realize this is the best way to build an HTGR we will gather the needed resources and demonstrate the technology.
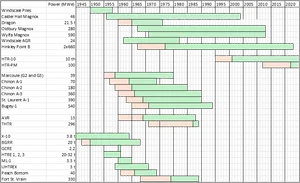
Starting an advanced reactor industry
Thoughts on moving from one-of-a-kind demos to fully fledged industry
As explored in depth by Stephen Ezell at ITIF, China is surpassing the U.S. and Europe in nuclear technology, and in order to compete, we may need a “whole of government” approach. To reestablish advanced reactor leadership, we need a long-term strategic vision that accounts for the specific challenges and opportunities of advanced reactors. Further, we need to lay the groundwork to create an entirely new industry, with new supply chains, business models, and technology, not just develop one-of-a-kind projects. What follows is inspired by the history of advanced reactor development and our own efforts to develop novel nuclear power technology.
Advanced reactor history: still on the way to 2nd-of-a-kind
Metal cooled reactor history
The first “usable” electricity from nuclear power was from a liquid metal cooled reactor, the Experimental Breeder Reactor I. Liquid metal reactors have used mercury, sodium, sodium-potassium eutectics, lead, or lead-bismuth eutectics to cool the core instead of water.
While these concepts showed promise, they have yet to scale. The closest it came to serial use was in the Alfa-class submarines in the Soviet Union, but they faced several challenges. The coolant was a lead-bismuth alloy, and the reactor design was technically compelling with higher operating temperatures making it more efficient and giving it a higher power density. However, the reactors were very difficult to maintain. Out of seven built, four had major issues, and the remaining units were all eventually decommissioned (if sinking to the ocean floor counts as decommissioning…).
Outside of these submarines, liquid metal reactors have mostly been one-of-a-kind projects. The U.S. built ~6 liquid metal reactors, none of which were commercial successes. France has a long term (multi-decade) reactor development program that stared with Rapsodie in the 1960s, then built Phenix, and finally Superphenix in the 1980s. France had intended to continue with another one-of-a-kind project, ASTRID, but this project was unfortunately cancelled in 2019. Russia has been working on the BN series reactors which have evolved from 5 to 800 MWe over 5 reactors and 50 years. The goal is that the BN-1200 will enter into “serial production” after demonstration in the mid-2030s.
The point here is that to develop an advanced reactor into a product ready for “serial production”, it took Russia 5 demonstration reactors over 70 years.
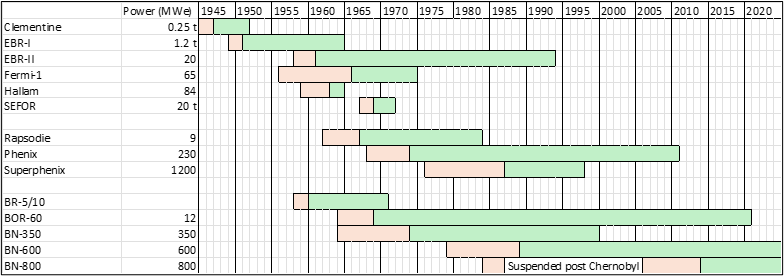
Gas cooled reactor history
Gas reactors were similarly explored in the early days of the industry. There have been reactors cooled with air, CO2, helium, and nitrogen. Several countries, including the United Kingdom, China, France, Germany, and the U.S., explored gas reactors through various research programs.
The first gas-cooled reactors in the UK, France, and the U.S. were simply air-cooled graphite piles. Examples include GLEEP (UK), G-1 (France), and CP-2 and X-10 (US). These later evolved into fully fledge reactor programs, but similar to the liquid metal reactor history, each reactor was a one-of-a-kind project. Even reactors carrying the same title, such as the AGRs were vastly different in internal architecture and engineering.
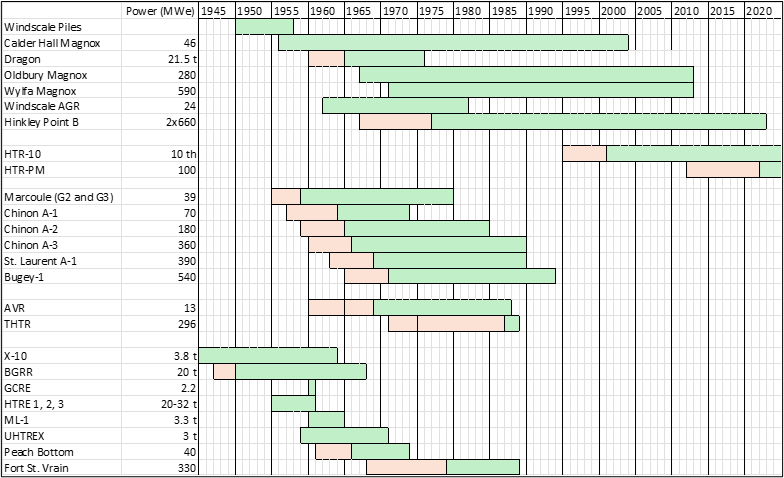
Other advanced reactors, like molten salt reactors, have not had the attention and deployment of gas and metal cooled reactors. The Molten Salt Reactor Experiment in Oak Ridge operated for 13,000 hours or less than two complete years. No scaled-up versions followed, although Oak Ridge did estimate the next demonstration reactor required for molten salt reactor development would have cost $2.5B in 2024 dollars.
We made these timeline charts to show just how much the industry was building and testing, and despite all of these efforts, light water reactors were still the only commercial success. If we want an advanced reactor industry, we need a similar level of building and testing.
Focus for the long-term
Success requires a long-term focus. Engineering is challenging, and the long-term view sharpens focus on solving the problems of today without diversion. In advanced reactor programs, apparent shortcuts can distract engineering teams when they are facing challenges. For example, the Next Generation Nuclear Plant program (NGNP) shifted internal focus to study printed circuit heat exchangers (PCHE) when facing the challenges of manufacturing large helical coil steam generators (HCSG). PCHEs have many attractive attributes, but there is no ASME code approved pathway to using them in nuclear reactors today. One could argue that the NGNP team should have focused on developing HCSG manufacturing capability which have better positioned the industry today as X-Energy is planning to use an HCSG.
The global reactor development experience shows us that going from concept to commercial takes at least 20 years with several prototype reactors along the way. Even still, after decades, these programs often shift focus to a new design or get cancelled. We are convinced that a focused, well-funded, multi-decade (less depending on funding) effort will be required to break this pattern and create an advanced reactor industry. This is what Idaho National Lab was built for!
Creating an industry, not a prototype
Creating an industry is much more than designing a reactor. We need new manufacturing capability, new fuel fabrication lines, novel regulatory approaches, new business models, suppliers for components, parts, services and more. The good news is that there are many startups in this space, and their collective capital and drive is larger than any one company’s drive could be. Third Way’s Advanced Nuclear Map shows 130 projects worldwide, and the slide below from the NRC shows over 30 in the U.S.
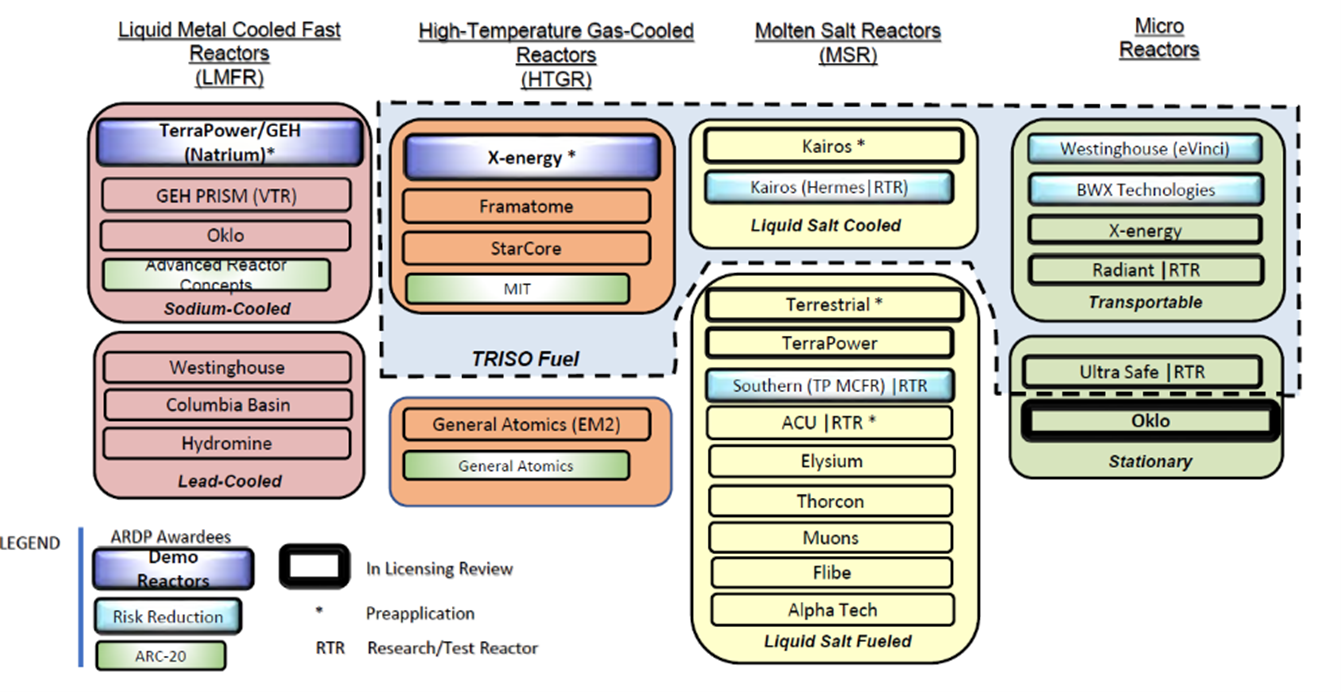
When focused on MIGHTR, we made the calculated decision that the outsized number of HTGRs among advanced reactor developers would be to our benefit – helping to seed the development of all parts of the necessary industry. We intentionally carved the <20 MWt range out of our original MIGHTR patent because we knew it would be useful if someone else was developing similar technology. For example, we faced several technical challenges, where we would have benefited from someone’s success:
Helical coil steam generator manufacturing
Printed circuit heat exchanger ASME code case development
Helium circulator development
Vessels, seals, and large-scale helium containment
Auxiliary tooling and robotics
The technology and regulatory success from ongoing HTGR projects will benefit the whole industry, and it could be a major turning point for HTGRs in the U.S. Success for the larger players is likely to help the early-stage companies as well.
How the advanced reactor industry can move faster
There are several forces already accelerating the creation of an industry:
The highest level of public support for nuclear in decades is creating new policy opportunities and easing siting concerns.
The Advance Act may create more industry and regulatory willingness to innovate in a way that accelerates deployment.
Risk informed licensing, either through the Licensing Modernization Project (Reg Guide 1.233) or 10 CFR Part 53, may create the environment for innovative safety cases or regulatory approaches, which may simplify licensing, development, and construction.
However, the advanced reactor community can likely move faster than it is, so it is useful to identify some of the forces that slow its development:
Total cost to design and engineer a novel power plant system is in the billions of dollars. Look forward to a future post on this topic.
Complex system integration creates project management challenges. These aren’t specific to nuclear. The extensive supply chain for the Boeing 787 was notorious for causing delays. SpaceX has had great success with vertical integration. Westinghouse’s tried to resolve some construction cost overruns at Vogtle and Summer through an acquisition of CB&I Stone & Webster. Just look at how extensive the TerraPower list of suppliers is.
Aversion to regulatory risk and licensing uncertainty. Design engineers see rejection as too high a cost to pay late in a project, so they design-in conservatism that sometimes is unnecessary. This can materialize in several ways: refusal to adopt a new code or method or assuming an LWR safety system is necessary for an advanced reactor, when in both cases the NRC has shown themselves to be innovative and flexible. However, there may be other cases where the extra conservativism was necessary to deal with licensing uncertainty that stemmed from early design uncertainty. This licensing uncertainty does not necessarily come from the NRC. It also comes from the inherent complexity in the design process internal to the reactor design organization.
On the integration, Kairos Power is vertically integrating to resolve this challenge, but others in the space are relying on a host of suppliers, so management will be key to their success. There is a lot of room for software development of configuration management tools to integrate suppliers.
On the regulatory risk, the nuclear community has an interesting culture of innovation. There are many advanced reactor startups bringing new ideas into the industry. However, their willingness to use different tools, license new materials, license new manufacturing methods, or present new safety cases to the regulator has been limited. In many of these areas, there is a huge reward for successfully delivering something novel, but also a huge risk of wasted time and money if you fail to deliver. Firms likely need to shield engineers and managers from the risks or reward them explicitly for the wins to encourage a new culture of innovation.
How to do tech selection
Selecting which projects to fund that maximize the industry’s success is a critical piece of the puzzle. The capital for developing advanced reactors should concentrate around the best advanced reactor projects which means we need methods for assessing the “best projects”. These selections should happen based on TRL, cost to deploy today, team capacity/credibility, market potential and other benefits.
Market potential can be assessed by considering the realistic market this technology could serve in the next 20+ years. This comes from identifying what markets could need nuclear power on that timescale. Process heat is a good example here.
In our view, technology readiness should be evaluated based on both past and present developments. While recent advancements might accelerate the maturation process, it is unlikely that any breakthrough in energy will enable the development and deployment of full nuclear technology, such as ARs or SMRs, at more than twice the historical rate. Considering that Water-Cooled Reactors took 40 years to mature in construction and operation, we estimate a timeframe of at least 20 years to achieve technological maturity and near-full economic potential from scratch. Technologies further along the development path may require less time, but this needs to be carefully judged for technology selection.
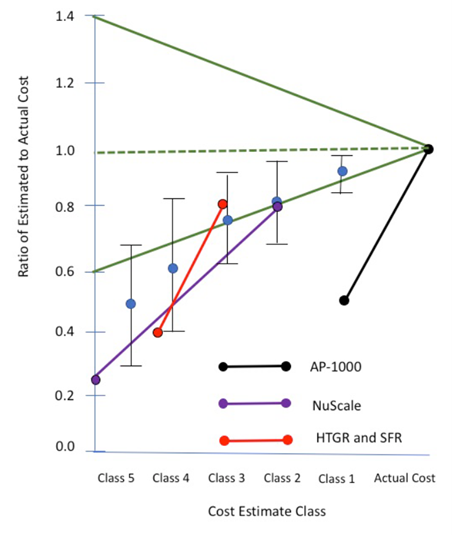
Estimating the cost of deployment today is complex. Detailed cost and timeline projections are not feasible until a design is fixed and detailed. However, high-order cost modeling techniques, based on footprints, building volumes, and main components, can provide preliminary estimates. It is crucial to remember that a cost estimate can only be as accurate as the design it is based on. Designs with attractive cost estimates but low TRL and early-stage plant designs are likely to be misleading. To mitigate this, we proposed a “develop by embodiment” strategy, as published in ANS, which significantly reduces the risk of unexpected design growth and cost overruns from the early days until the design is complete.
Because early cost estimates often underestimate final costs, the industry should explore low(er) cost pathways to increase the accuracy of these modeling efforts. One option is increased non-nuclear system demonstrations to prove manufacturability, constructability, and operability. This can be coupled with an independent design review on licensability. Together, this could get a reasonable look at the comparable costs between different technologies without requiring expensive FOAK nuclear projects.
Concluding remarks
Advanced reactors will face many of the same issues that light water reactors do, and there is a lot of knowledge and experience to share between the communities. There are a few key elements we observe in other countries with healthy advanced reactor programs:
A thriving light water reactor industry
Russia has 20 VVERs under construction globally
China has 17 total HPR1000s and CAP1000 under construction
Long term funding continuity over decades.
Technical focus on bringing a single reactor type to completion before pivoting.
Paired with wise technology selection, we believe there is a path to a thriving advanced nuclear industry.
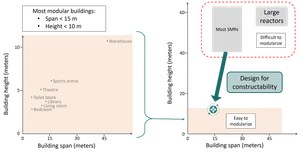
Introducing Boston Atomics
Who?
Boston Atomics is a nuclear R&D firm. As experienced advanced reactor designers, we offer insights in system integration, techno-economic analysis, and technology barriers and opportunities for advanced reactors. Our vision is to foster a policy, regulatory, and technical environment that enables advanced reactors to scale and thrive.
We work with our partners to develop cost-reducing technology for new nuclear and provide consulting services to the broader energy industry. In early reactor conceptualization, single technical disciplines often dominate the design philosophy at the cost of other disciplines. This makes realizing performance improvements challenging because changes that improve one dimension often hinder others.
At Boston Atomics, we employ a multi-disciplinary approach, allowing us to more readily identify innovations with realizable benefits. This holistic perspective enables us to see the broader picture of the advanced reactor landscape. Through this blog, we aim to explore and discuss the necessary technological and regulatory developments that will propel the advanced reactor community forward. Our goal is to contribute to the field's evolution from isolated, one-of-a-kind projects to a robust, scalable industry.
Design for constructability
Through reconciling disparate fields: civil and nuclear engineering, we invented a novel reactor concept called MIGHTR. MIGHTR introduces a unique approach to exploiting modular construction techniques for nuclear systems.
It was born from the idea that constructability needs an equal place among other objectives in early reactor conceptualization. Advanced reactors (ARs) and small modular reactors (SMRs), because of their lost economy of scale, need paradigm shifting innovation – ideas that shift the cost curve, not just optimize down the curve.
The MIGHTR concept integrates the largest components of High Temperature Gas Reactors (HTGRs) and rotates them from a vertical orientation to a horizontal one. Under a subcontract through MIT, we embarked on a DOE funded 3 year, $4.9M effort to evaluate the safety systems, main components, core physics, and thermal fluids of our new architecture, which included collaborators from University of Michigan, Argonne National Lab, MPR, and SGH. We continue to incubate MIGHTR in collaboration with universities and national labs, and our website has links to all the publications describing our progress.
Our work developing MIGHTR demonstrates why we believe in designing-for-constructability from the beginning. Civil structures dictate the pace and cost of nuclear construction, so design for constructability is a winning approach, but it typically enters the design process too late, after much of the design architecture is fixed. By this time, you are working down the value engineering curve, not shifting it to unlock real cost reductions.
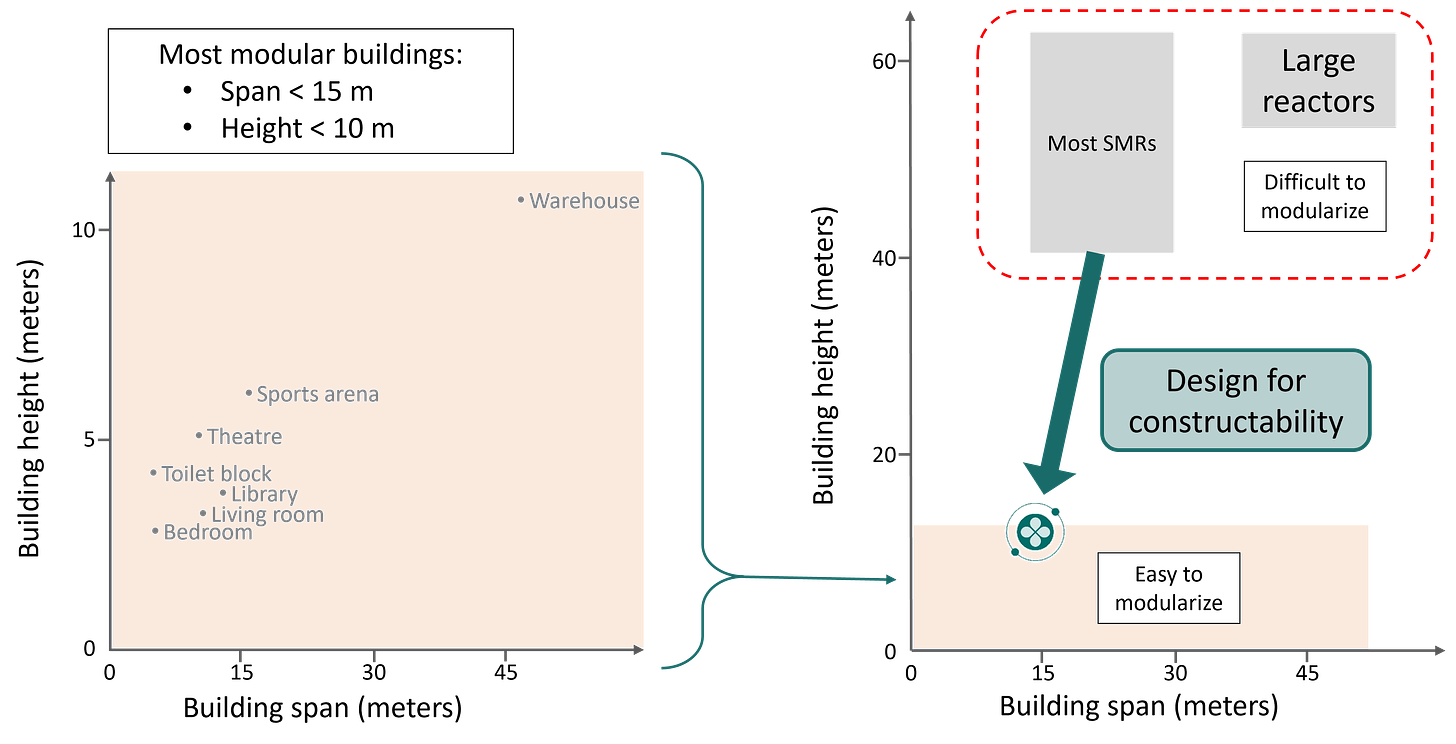
At the height of nuclear construction in the U.S., United Engineers and Constructors published a report on nuclear plant construction costs, and they stated:
The most significant factor dictating construction sequence is gravity. By investigating elimination of the vertical component in plant arrangement, it is possible to substantially change the sequence of erection. The reduction of the vertical component has a further advantageous effect in that it reduces lifting requirements, vertical access for crafts, and related safety and indirect cost considerations.
The potential of our approach is uncertain, but as part of the ARC-20 project we estimated the cost savings to be on the order of 30%.
What is clear, however, is that we are going to hear extensively about the need for value engineering and constructability for ARs and SMRs. That work will be critical, and how well each reactor architecture and firm can value engineer their way down the cost curve will determine their success.
Why an HTGR?
HTGRs are a great complement to water cooled reactors (WCR), because of their relative technology maturity, global development effort, and market opportunity in industrial process heat.
The global HTGR coalition
HTGRs, like many advanced reactors, have many attractive features: passive safety systems, high temperature output and thermal efficiency, reduced emergency evacuation zones, and others. Relative to WCRs, however, they are technologically immature and with nascent supply chains and regulatory readiness. According to the IAEA, today’s global WCR supply chain services >400 reactors, and WCRs are 94% of reactors in construction. Therefore, when selecting an advanced reactor to develop, we wanted to choose one with global development inertia.
The last three decades have seen significant investment in HTGR technology:
The experimental HTR-10 in China (design in 1992, construction in 1995, operation started in 2003)
The commercial demonstration HTR-PM in China (design in 2001, construction in 2012, operation started in 2023)
The Next Generation Nuclear Plant (NGNP) R&D program in the U.S. made progress in regulatory readiness and fuel development.
The GEMINI Initiative and NC2I in Europe focuses on design, fuel supply chain, regulatory readiness, and customer demand.
Commercial ventures: X-Energy, Ultra Safe Nuclear Corp, Radiant Nuclear, and others
The advanced reactor program in France supporting Jimmy
The pebble bed modular reactor program in South Africa
The broad coalition of HTGR development meant that the supply chain, regulation, and technology readiness were outsized relative to other advanced reactor technology, and the odds of commercial success were substantially higher. Further, all the recent deployments of HTGRs have taken place in China, making it in the strategic national interest to develop this capability in the U.S.
In the same vein, we knew that the operational performance of advanced reactors has historically been worse than the water-cooled fleet. Therefore, we wanted to select a coolant with substantial operating history. Water-cooled reactors dominate the global operating experience with 90% of the commercial reactor-years, but gas-cooled reactors have more than 9X the experience that metal-cooled reactors do.
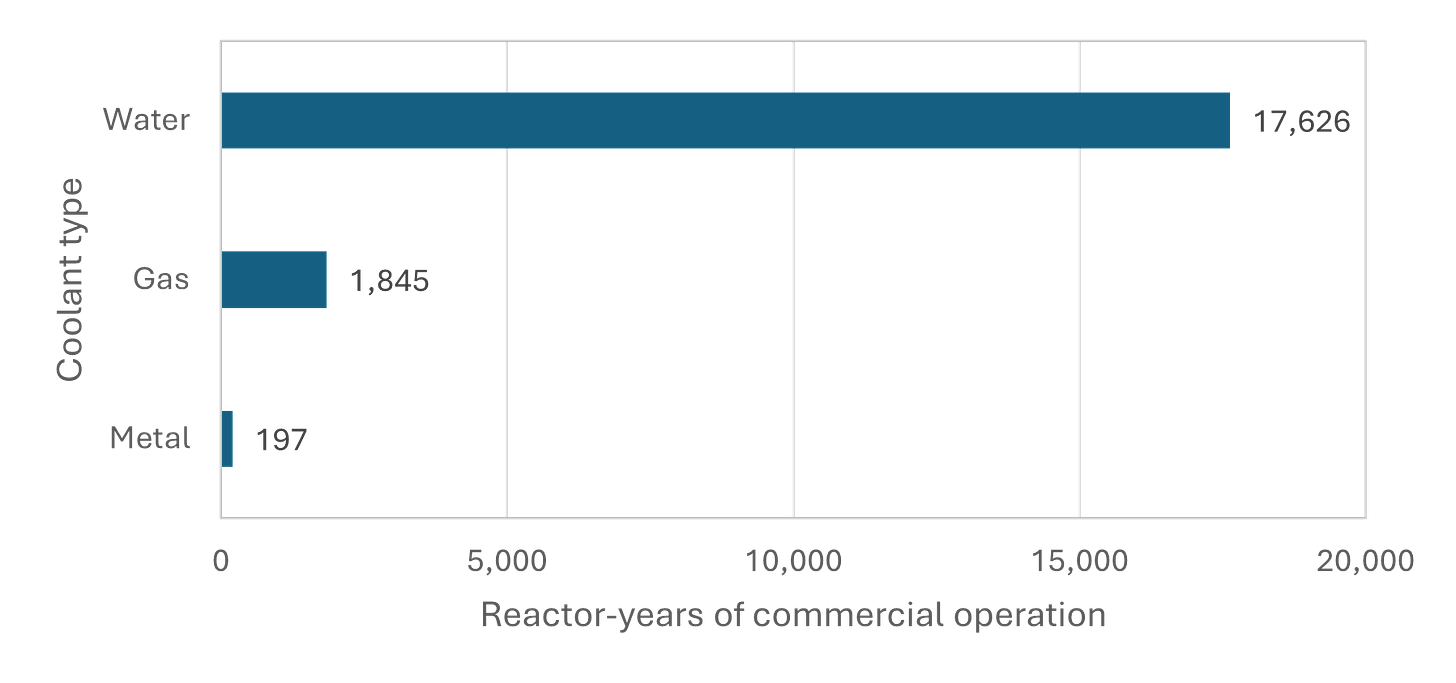
Process heat - valuable market opportunity
In the effort to decarbonize our economy, industrial process heat is an enormous challenge and therefore an opportunity. In a report on Low Carbon Heat Solutions, the Columbia Center on Global Energy Policy found that nuclear could offer the lowest cost source of zero-emission heat for certain temperature ranges. Nuclear power produces heat that is converted to electricity at ~33% efficiency, so if nuclear plants sold heat directly, it would reduce the cost per unit of energy by 1/3. This gives nuclear a strong economic advantage over electrified heat from renewable sources.
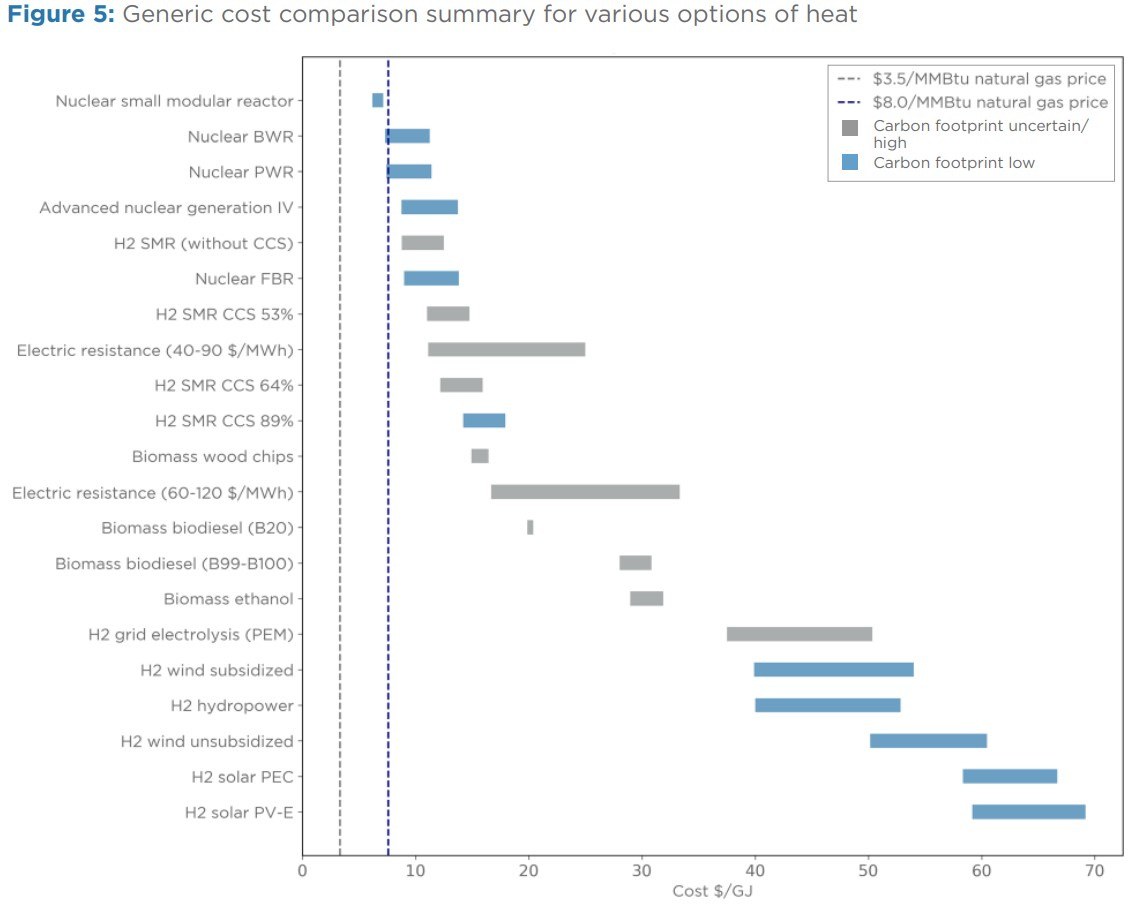
Historically, HTGRs have had the highest reactor outlet temperatures which will give them the most flexibility to meet the various demand cases. The HTTR in Japan is famous for a jaw-dropping 950°C core outlet temperature. In the ranges achievable for nuclear, there is almost 2X the demand for heat greater than 250°C than below which opens a much larger market size for high temperature reactors. The combination of the expected growing demand for zero-carbon high temperature heat and intrinsic cost advantage made a compelling case for HTGRs.
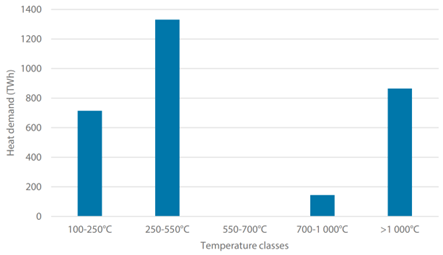
Slowing down MIGHTR activities…for now
From the beginning we said that we needed at least $1B in design and engineering before starting construction. Here is a screenshot from our first pitch deck in 2022. This was certainly sub-optimal from a fundraising perspective, but we wanted to partner with folks who had a realistic picture of what was required to deploy an advanced reactor.
In 2023, we did more in-depth planning, and we saw this was a lower bound. We are working on a future post that discusses the cost of designing multi-disciplinary machines, but in short, the NuScale plant and the AP1000 were both ~$1.5B design efforts, and they were incremental steps in pressurized water reactors. Advanced reactors are much more nascent, and lack active supply chains, and therefore we believe have higher development costs in today’s world.
Finally, the MIGHTR cost advantage was over other HTGRs, not LWRs. It is unclear if MIGHTR is cost-competitive with LWRs, or if any advanced reactor can be. There is a world where advanced reactors are equal or lower cost than LWRs, but it probably isn’t here yet, and until it is, we think capital should consolidate around deploying LWRs and developing the best advanced reactor concepts. In a future post we will discuss what needs to be true for advanced reactors to provide cheap, abundant power, and how to select the projects that would most likely affordably deploy advanced nuclear energy. Regarding MIGHTR, what we can say now is that we don’t expect to demonstrate any fueled version before the late 2030s.
Let’s work together
We transitioned Boston Atomics from a reactor development company to a nuclear R&D and consulting practice, with specialties in systems integration and techno-economic assessment for nuclear systems. In that vein, we have already partnered with national labs, universities, governments, reactor developers, and utilities. Reach out if you are interested.
In parallel, we are planning follow-up posts on topics like:
The cost to design complex machines
Kickstarting an advanced reactor industry
What’s needed for advanced reactors to be cost-competitive
The MIGHTR project
If you are in the advanced reactor ecosystem and have a topic that you have been itching to write about, please reach out: info@bostonatomics.com.